3 Ways to Stop Money Leaks in Your Coating Installation Business
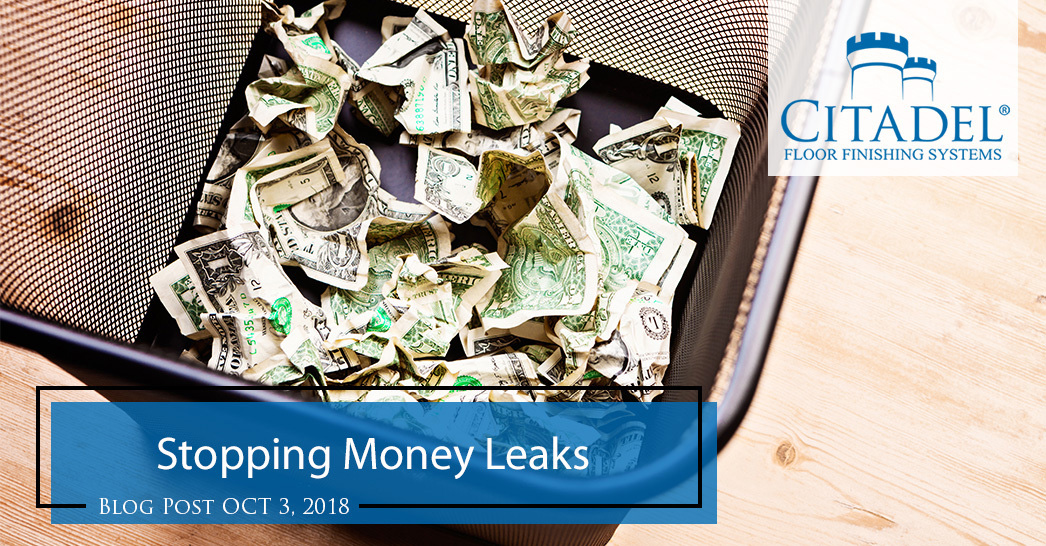
2018-10-03
1 – Inaccurate bids
Are your bids covering all your business costs (and then some)? According to George Hedley’s article on ConstructionBusinessOwner.com, “Most companies don’t know their current, exact overhead markup rate.” Overhead includes the expenses it takes to run the business, outside direct job costs. How to bid better:
- Calculate your markup rate by dividing overhead expenses by projected job costs for the year so you cover those costs in each bid.
- Track the square footage one team member can surface prep, profile or coat per hour on a typical job to get a better sense of labor expectations.
- Review final costs against the original estimate upon each job’s completion to for a reality check. (Did your costs run as you expected them to?)
- Create a system: develop an estimating checklist of all items required (and often missed) when bidding projects.
2 – Budget overruns
Bringing a project to completion on time and on budget is no small feat. Team leads are often too busy with scheduling, logistics and customers to focus on keeping costs in line. How to stay on budget:
- Assign responsibility for achieving budget goals to a specific role in the company.
- Implement a job cost scorecard tracking system and regular meetings to review results.
- Set field systems and company standards, with guidelines around equipment maintenance, tool management, inventory, job hours, start and finish times, break time standards, cleanup, etc.
- Don’t allow overtime unless it’s in the budget and approved, and assign labor strategically – so the low man on the totem pole makes an emergency supply run, rather than the supervisor.
3 – Inefficient operations
Are your installers working as efficiently as they can? Are there opportunities for cost and time savings in your current processes.
- Review existing workflows and notice when time or materials go to waste, and identify duplications, unnecessary delays and other opportunities to streamline.
- Implement systems to keep your installation team on track. Create standards for surface prep, cleaning and repair, profiling, and coating system application among other processes.
- Use labor-efficient materials. Polyurea is easier to apply, and cures quicker than other polymer-based coatings, reducing your team’s downtime—and lowering overall labor costs.
- Choose cost-effective materials. Look beyond price per gallon, to the true cost per square foot.
Ready to review your current operations and materials to stop money leaks? Our flooring experts can help answer your questions on the most efficient and cost-effective materials on the market—and help you choose the best product for each installation. Schedule your chat with a flooring expert today.
Latest News
How to Maintain Your Concrete Grinder
Gain Customers and Referrals in 4 Easy Steps
Ready for the Summer Rush? 4 Ways to Prepare
6 Cold Weather Safety Tips for Installers
How to Remove Salt Stains from Concrete
Testimonials
Every time I call I get to talk to someone, and I always have an answer within 20 minutes. That's awesome.
Client: Terry C.